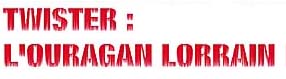
On parle depuis longtemps de "la" soufflerie de Nancy-Azelot. Arlésienne pour certains, pourtant la rumeur des premiers essais et d'une prochaine ouverture a déjà fait le tour des oreilles parachutistes françaises (et catalanes...). Aujourd'hui, Philippe et Vincent Mengel (respectivement père et fils), qui l'ont rêvée, puis réalisée, font le point avec ParaMag sur ce qu'on ne peut plus manquer à dix kilomètres du centre : Twister...
P r o p o s r e c u e i l l i s p a r G i l l e s D e f o u r n e a u x, le 20/04/99
P h o t o s : B r u n o P a s s e, M i c h e l A l l o t
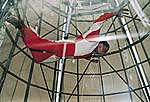
ParaMag : Une histoire, qui comme souvent est née, un beau jour, sans prévenir...
Philippe Mengel : J'ai commencé le parachutisme sportif en 1991, en fin de saison (septembre) par une progression traditionnelle. Cette année-là, j'ai fait huit sauts ! Cause météo, vent, etc... Bref, j'ai failli arrèter un peu dégoûté. J'ai donc eu le temps nécessaire pour réfléchir (entre deux sauts) sur les moyens qui permettraient de moderniser et surtout d'accélérer l'enseignement du parachutisme.
Le meilleur moyen était de pouvoir recréer au sol les conditions nécessaires pour simuler la chute libre. Dominique Boulanger m'a laissé entendre que cette pratique était utilisée aux U.S.A., et qu'elle avait beaucoup d'avantages. Analyse faite, je me suis rendu compte qu'en plus, la soufflerie permettrait de recruter plus facilement, qu'elle permettrait également d'occuper les pratiquants en cas de mauvais temps, et qu'elle allongerait certainement la saison de sauts trop courte dans nos régions. Je me suis donc lancé le défi de construire la première soufflerie française...
ParaMag : C'est ici que commencent les grands travaux.
Philippe : Pour ce faire, je me suis rapproché de l'E.S.T.I.N.N. de Nancy, école supérieure avec laquelle j'ai de fréquentes relations par mon entreprise E.C.V.I. Perpétuellement en recherche de sujets d'études, cette école a accepté de me prêter main-forte, notamment en ce qui concerne le dimensionnement, l'évaluation des puissances, la numérisation des écoulements (nous sommes tombés au coeur d'un débat scientifique, opposant les partisans de la modélisation informatique, et ceux du modètle réduit), et enfin le calcul des structures. Le plus dur a été de mettre en corrélation les moyens techniques que nous avons à notre portée avec les exigences des étudiants. Notre souhait était en effet d'utiliser des dérivés du Poids Lourd pour obtenir un prix de réalisation abordable. Pour ma part, j'ai réalisé tous les plans d'ensemble et les plans de détail sur D.A.O. Ces études ont duré trois ans.
ParaMag : Qui sont les artisans de cette réalisation ?.
Philippe : La construction a été entièrement réalisée par moi- même, Vincent, et Sébastien Blaise, un cousin, en trois ans.
ParaMag : Twister est donc unique, quelles sont ces idées que vous vouliez implémenter ?
Philippe : On trouve dans le monde trois types principaux de souffleries : flux libre, flux semi-guidé, et flux guidé. Chacun de ces principes a ses avantages et ses inconvénients. Dans le cas d'un flux libre (Zurich, par exemple), la puissance est très limitée, on ne peut pas monter haut dans la masse d'air. Dans le cas d'un flux complètement guidé (Fort Bragg), l'air qui est accéléré par les hélices est réutilisé. Il est reconduit de la sortie de la veine vers l'admission d'air. Mais, à moins de construire un bâtiment gigantesque, profilé exactement pour canaliser les déplacements de grosses masses d'air lentement, tout le gain espéré est en fait perdu à cause des frottements sur les "coudes" de la structure. De plus, la température devient rapidement intenable, et il faut des systèmes réfrigérants encore plus bruyants que la soufflerie elle- même ! Nous avons donc choisi de nous orienter vers un principe de flux semi-guidé, à partir duquel nous avons élaboré Twister.
ParaMag : Nous voilà maintenant devant un géant de plus de vingt mètres de haut, l'air est aspiré dans une fosse, et après ?
Vincent Mengel : Au départ la soufflerie c'était un énorme trou de vingt mètres de diamètre et de six mètres cinquante de profondeur, sur lequel la veine d'air est supportée par une charpente de vingt-deux mètres de haut. Au fond du trou, il y a trois moteurs diesel, quatre cent chevaux chacun, avec des énormes cardans et des renvois par courroie aux hélices. Ce sont des hélices de six pales que l'on a faites faire spécialement par un hélicier. Au total ça fait dix-huit pales, donc il y a de quoi brasser !
Ensuite cet air est propulsé dans un convergent. Ce convergent va avoir pour but de provoquer un effet Venturi, donc une accélération de l'air, et à mi-convergent, l'air va passer dans un redresseur d'air pour avoir un flux laminaire. Sinon, on a de l'air qui tourne constamment dans le tube, en chute on serait tout le temps en train de tourner. Passé le convergent, on va aller sur un divergent, une énorme manche à air à l'envers, c'est-à-dire que plus on monte, plus le diamètre de chute est important. La première partie, jusqu'à huit mètres au-dessus du sol, est toute en plexi, transparente, puis après on disparaît dans une bâche jusqu'en haut.
ParaMag : Ca donne quels espaces ?
Vincent :La porte de la soufflerie se situe à six mètres cinquante au-dessus de la dalle. On entre sur un filet, au niveau de la fin du convergent. A l'embase, au niveau du filet, on est à un peu plus de trois mètres cinquante de diamètre, en haut du divergent, on est à déjà plus de quatre mètres, et vraiment tout en haut, on a plus de cinq mètres de diamètre.
.../...
Retrouver
la suite de cet article...?
|